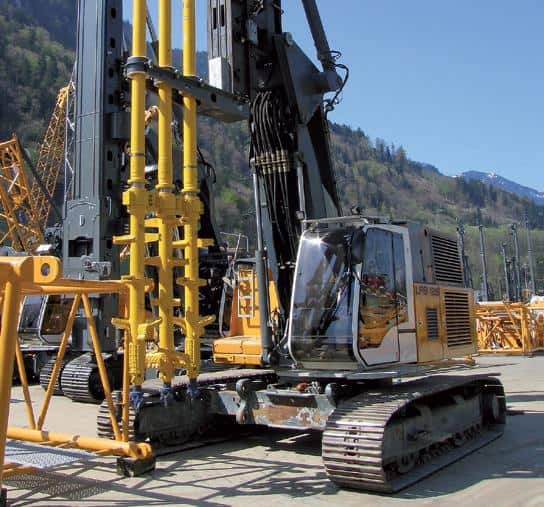
Triple-axis continuous flight auger
Deep Soil Mixing?
Deep Soil Mixing: The properties of soft cohesive soils can be improved by mixing of a variety of chemical additives. The addition of lime, fly ash and cement in different combinations can significantly improve the shear strength and compression properties of such soils. Other additives can be used to fix pollutants in place to prevent leaching or to reduce soil permeability. Deep soil mixing (DSM) is achieved using either a wet or a dry process where metered quantities of additives are injected into the soil through the hollow stem of a rotary drill string fitted to a drilling rig.
In Simple Words “It is a soil mixing method used in holding back earth or stabilizing the soil, even before excavation commences.”
The method helps to achieve significant improvement of mechanical and physical properties of the existing soil, which after mixing with cement or compound binders becomes the so-called soil-mix (or soil-cement). The stabilized soil material that is produced has a higher strength, lower permeability and lower compressibility than the native soil.
Wet and Dry mixing
There are two different mixing methods of deep soil mixing. The existing soil which has to be improved can be mixed mechanically, either with a slurry including binder (wet DSM) or with a dry binder (dry DSM). Jetting of slurry can be also used to boost the mechanical mixing.
The wet method is more appropriate in soft clays, silts and fine-grained sands with lower water content and in stratified ground conditions including interbedded soft and stiff or dense soil layers. The dry method is more suitable for soft soils with very high moisture content, and hence appropriate for mixing with dry binders.
Typical Applications
- Embankments on soft soils.
- Support of strip, pad and slab foundations
- Bridge and wind turbine foundations
- Excavation protection walls using reinforced columns
- Slope stabilization.
- Mitigation of liquefaction potential
- Cut-off walls and barriers
- Environmental stabilization and solidification
Wet Deep Soil Mixing method
This method consists of a special mixing tool which is inserted into the soil on site. This mixing tool comprises of a drilling rod, transverse beams and a drill end with a head. The drilling does not cause any vibrations, and is accommodated by cement slurry outflow from nozzles intentionally placed at the end of the soil auger. When the design depth is reached, the construction phase of deep soil mixing (DSM) columns is started.
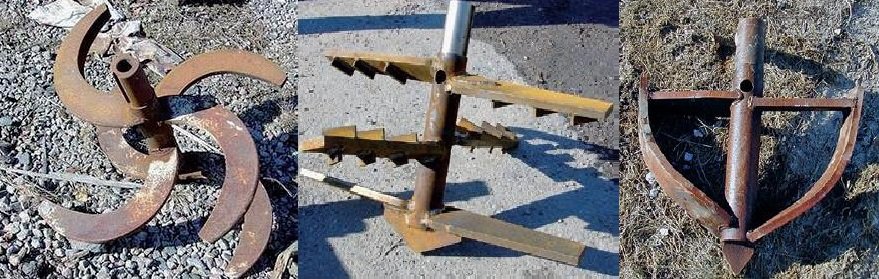
Mass wet soil mixing is carried out with a horizontal axis rotary mixing tool at the end of a track hoe arm. The binder slurry is injected through a feed pipe which is attached to the arm.
This technique creates individual soilcrete columns, rows of overlapping columns, all of which have a specific design strength and stiffness. Wet soil mixing is suitable to any soil types which includes even organic soil. With this method, the treatment of soil is possible to depths up to 100 feet.
Dry Deep Soil Mixing method
Dry soil mixing is a ground improvement technique that mechanically mixes the soil with dry cementitious binder to create soilcrete so as to improve the weak soils such as soft, high moisture clays, peats. A high speed drill moves into the ground with a drill rod which has radial mixing paddles near the bottom so as to construct the columns. During the penetration of the tool into the ground, it shears the soils to prepare them for mixing. As and when the tool the specified design depth, the binder is injected through the drill steel where it is assorted with the soil as the tool is taken out.
Mass dry soil mixing is carried out with a horizontal axis rotating mixing tool positioned on the end of a track hoe arm. The binder is injected to the soil mixing tool through a feed pipe, which is attached to the track hoe arm. With dry soil mixing, the treatment for the soil is possible to depths up to 60 feet. Obstructions are sometimes pre-drilled ahead of the soil mixing process.
Triple-axis continuous flight auger Types
- Auger mix paddles
- triple-axis auger
- triple axis Cement Deep Soil Mix
multiple auger, paddle shafts
Mechanical soil mixing is performed using single or multiple shafts of augers and mixing paddles. The auger is slowly rotated into the ground, typically at 10-20 rpm, and advanced at 2 to 5 ft (0.5 to 1.5 m) per minute.
Retaining wall with bauer RG ,cut-off wall with bauger BG
The Deep Soil Mixing (DSM or Wet Soil Mixing method) is an in situ soil treatment technology whereby the soil is blended with cementitious and/or other materials, in order to improve bearing capacity of soil. The cementitious slurry is prepared in automatic mixing plant, s or in compact Grouting Sets . Once the slurry is mixed, it is pumped to a drilling hollow auger and mixed with soil at great depths. The complete soil mixing process is monitored and registered with the help of special software, such as Soil Mixing Master, developed by MODEL&CO. The process starts with drilling with low flow, once the auger reach maximum depth, it is withdrawn and higher slurry flow is pumped and mixed with soil until the required soil-slurry mixing ratio is reached.SOIL MIX WALLSoil mixing is used for temporary and permanent deep excavation projects. The method is used to mix cement slurry with soil in situ to create a cohesive soil block. Strength of mixed soil is variable and tailored according to project requirements and site conditions.
Mechanical soil mixing is performed using single or multiple shafts of augers and mixing paddles. The auger is slowly rotated into the ground. Cement slurry is pumped through the hollow stem of the shaft(s) feeding out at the tip of the auger as the auger advances. Mixing paddles are arrayed along the shaft above the auger to provide mixing and blending of the slurry and soil. Slurry lubricates the tool and assists in the breaking up of the soil into smaller pieces. Spoils come to the surface since fluid volume is being introduced into the ground. These spoils comprise cement slurry and soil particles with similar cement content as what remains in the ground. Pre-determined mixing patterns are followed to meet design requirements