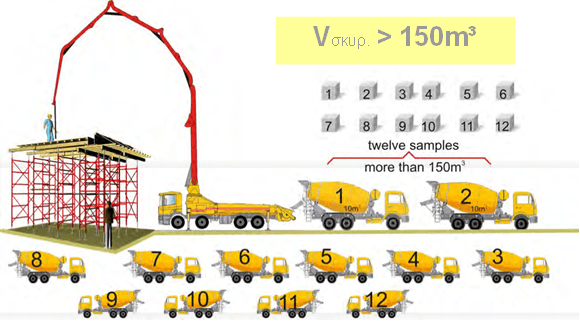
Concrete
General information
Concrete is composed by pitchers, gravels, sand, cement and water. It is created by blending these materials in measured amounts and stirring the mixture for a short period of time. The concrete’s main characteristic is the fact that it hardens within a few hours from its casting; moreover it gains a large amount of strength over the initial following days. Depending upon ad- ditional properties that the concrete is required to have, special admixtures may be added dur- ing the mixing process. These may be retarding admixtures or/and super-plasticizers for improv- ing concrete’s workability or even steel or other composite fibers in order to increase the mix- ture’s compressive and tensile strength.
The classification of concrete grades is based on their compressive strength. Each concrete grade (Concrete) e.g. C25/30 is characterized by two equivalent strengths, which in this specific
example are 25MPa and 30MPa. The first is the characteristic strength fck of a standard con- crete cylinder4 and the latter is the characteristic strength of a standard concrete cube.
The concrete grades mentioned in Eurocode5 2 and EN 206-1, are:
C12/15 |
C16/20 |
C20/25 |
C25/30 |
C30/37 |
C35/45 |
C40/50 |
C45/55 |
C50/60 |
C55/67 |
C60/75 |
C70/85 |
C80/95 |
C95/105 |
4 This is the compressive strength used in the design
5 In ΕKOS 2000 and CTR-97, the mentioned concrete grades are up to C50/60
In Greece, old types of concrete (B) were being used, systematically until 1994 and periodically until 1997. The most commonly used was Β160 (corresponding to today’s C12/15), Β225 (cor- responding to an intermediate grade between today’s C12/15 and C16/20) and Β300 (almost corresponding to today’s C20/25).
Note:
The regulations and practices mentioned below refer to the Greek CTR-97 (Concrete Technol- ogy Regulation, 1997). This Regulation is valid, in this transitional stage, along with the Euro- pean Standard EN 206-1. The European Standard EN 206-1 is more advanced and has trans- ferred a great amount of responsibility that had to do with building-site procedures, like concrete sampling, to the concrete supplier who of course must be properly certified.
The amount of cement used in the mixture, should be enough not only to ensure the required concrete strength but also, in relation to the concrete’s use, to ensure its life span durability de- pended upon the surrounding present conditions:
use of concrete |
usual |
without finishing |
Seaside location (<1km) |
Inside water |
Inside sea water |
Other cases |
Cement (kg/m3) |
270 |
300 |
330 |
350 |
400 |
it depends |
Adding water to the concrete mixture beyond a specified point, results in lowering its strength and increasing its porosity. The proper amount of water is depended not only upon the required strength but also upon the required workability of concrete, as a matter of fact, the later is the one that basically determines that amount. The workability of concrete is determined by the slump height s.
Depending upon its use, concrete must have a slump height ranging between specific target values. These target values are shown below:
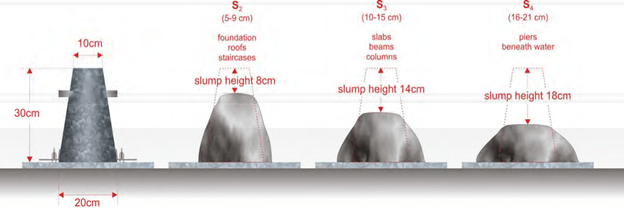
Ordering concrete
When ordering a pre-mixed concrete we must give the supplier at least the following informa- tion:
- Quantity in cubic meters: e.g. 60m³
- Concrete grade e.g. C20/25
- Minimum amount of cement6: e.g. 300kg/m³
- Slump class S 7: e.g. S3
- Super-plasticizer: e.g. YES (placed on order at the building site) 8
- Pump’s size: e.g. 36 m
- Time between truckloads: e.g. every 30 minutes
- Slump class S 7: e.g. S3
6 If the concrete’s grade e.g. C30/37, adequately covers the required amount of cement, there is no need to mention its minimum amount.
7 In concrete containing 4th generation super-plasticizers, the desirable slump value is always exceeded.
8 see paragraph 2.4.4
Concrete arriving on site
In every in-transit concrete mixer that arrives at the construction site one must always check that the dispatch note corresponds to the given order. Special attention must be paid to the ex- act time of the mixer’s charging so as to ensure that between the completion of the casting and the charging, the elapsed time is lesser than two hours.
In case it is required to inspect the amount of concrete inside the mixing drum, one must always bear in mind that the concrete’s unit weight usually ranges between 2360 and 2400 kg/m³. This means that a 10m³ mixing drum has a net weight varying from 23.6 to 24.0t.
The concrete’s strength is confirmed by sample testing. According to the regulation the mini- mum number of test samples to be taken in the concreting process, depends upon the total amount of casted concrete:
- For an amount of concrete lesser than 20m³, 3 test samples must be taken from different mixing drums.
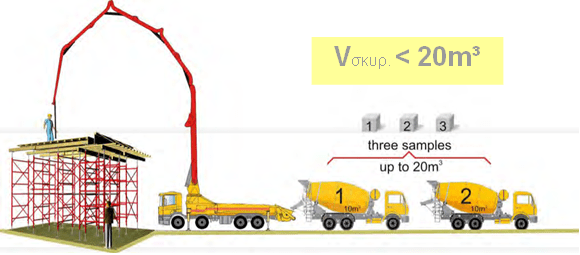
- For an amount of concrete ranging from 20m³ to 150m³, 6 test samples must be taken from 6 different drum mixers.
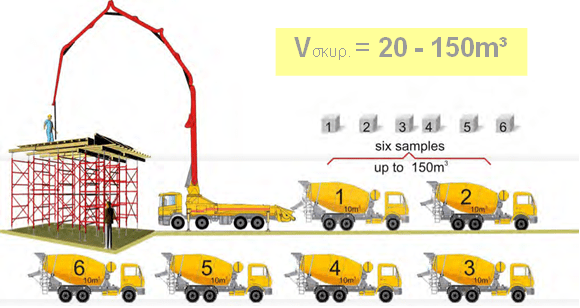
- For an amount of concrete greater than 150m³, 12 samples must be taken from 12 dif- ferent drum mixers.
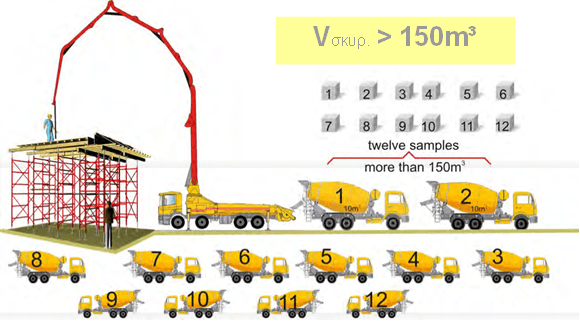
Samples must be taken from different in-transit concrete mixers and must be transferred to a certified laboratory for special curing within 20 to 32 hours.
Concrete pumping
Adding water to an already made concrete mixture may increase its workability but at the same time it lowers its strength. However, concrete must be workable enough to efficiently pass be- tween the narrow spaced steel reinforcement. This is achieved by use of a super-plasticizer added (1.5 to 2.0 kg/m³) inside the drum containing the wet concrete mixture before its dis- charge and mixed for 3 to 5 minutes in high rotating speed (8-12 R.P.M.).
Generally, the concrete used for the casting of foundation footings does not require a high level of workability and therefore adding a super-plasticizer is not necessary. On the other hand, in strip foundation, usage of super-plasticizer may be required when casting the pedestal, some- thing always done after the completion of the footing’s concreting. Finally when casting stair- cases (or sloped slabs) super-plasticizers should be avoided because the workable concrete flows towards only one side of the formwork.
Concrete casting
The first thing prior to casting is to thoroughly clear the formworks from dust, oil, etc. This should be done not only to ensure the building’s strength but also to set a technical-social example, in other words to set an example of professional behavior for all people working in the building site.
Concrete’s casting must be done directly from the pump’s hose end. The concrete must be purred inside the slab’s formwork in vertical and not horizontal layers. This happens because in case concreting has to be stopped for a long period of time, when it is resumed the new con- crete will not bind with the old one and a horizontal joint will be created. On the other hand, when concrete fills the formwork parallel to the thickness axis, a potential stop in casting will lead to the creation of a vertical joint.
The boom’s hose end should be around 0.50m above the formwork of the element to be casted. An exception can be made for usual columns and shear walls, where it can be up to 2.50m above the column’s bottom side. In cases where columns or shear walls have a relatively large height e.g. 5.0 m, concreting must be done by one of the following ways:
- The boom’s hose end is positioned in an adequate depth inside the column’s formwork,
- Extra pipes are placed from the upper part of the column to an adequate depth and con- crete is purred through them with the use of a special funnel.
- Openings with adequate size are created e.g. around the middle of the formwork and the concrete is casted through them (technically challenging procedure).
The (a) and (b) procedures are more practical but they require a certain amount of space. For example when using the boom’s hose end this space must have a diameter around 18cm and when using the extra pipes this diameter is decreased to 16cm. The required space can be pro- vided only if columns’ casting is performed separately from the rest of the elements. This means that concreting should not be done simultaneously in columns, beams and slabs with the use of one unified formwork. In earthquake prone regions simultaneous concreting should be avoided for one more reason: columns have a large amount of stiffness and therefore they are used for securing the position of formworks and scaffolds in cases of seismic events both during the casting and the curing process of the beams’ and slabs’ concrete.
Compacting concrete
Generally, concrete compaction should be carried out with the use of a vibrator. Two vibrating devices must be used regardless of the concrete to be casted. Based on the fact that one vibra- tor, serves around 5 to 10 m³ of concrete per hour, we calculate the required number of devices. For instance, when casting 100m³ of concrete in 6 hours time, we will need from 100/10/6=1.6 up to 100/5/6=3.2 vibrators, i.e. practically 3 vibrators are needed. When casting a small quan- tity of concrete e.g. 20m³, in 4 hours, theoretically one vibrator is enough, however having a backup device is mandatory for security reasons. Nowadays, the best solution is to use light- weight electric vibrators that ensure both high production rates due to their ease of operation and a high vibration quality which is very important especially in visible concrete surfaces (off- form concrete, architectural concrete)
Concrete curing
Concrete curing is mandatory. As a matter of fact, the higher the environmental temperature is, the more meticulously it has to be made. In every case, concrete’s surface has to be moistened throughout the entire day for at least the first week after casting; however the curing process will last for 28 days.
Concrete curing in extremely high temperatures can be done in three ways:
-
Right after finishing the concrete’s surface, we cover it with special sheets (burlaps). These sheets must be kept wet 24 hours a day for at least one week. Special attention must be paid to hold them down and prevent them from being blown away.
-
By ponding. We form a dam a few centimeters high (4 to 5 centimeters) around the pe- rimeter of the slab right after concreting. We fill this dam with water thus creating a pond and we make sure to replace water loses due to vaporization. The circumferential dam may be constructed with bricks cut in half or simply with fast curing cementious mortar. This solution has two disadvantages: it is not economical and it stops all works on the top of the slab for at least 7 days.
-
We spray the concrete’s wet surface with a special chemical fluid that becomes a membrane thus preventing concrete from drying out. This is the simplest procedure but in order to be effective, the concrete’s surface must be free from grooves created by a manually operated screed board. This can be achieved only with the use of a mechanic screed board that com- pacts the concrete as it vibrates. Without doubt, concrete casting must be done with the best possible conditions i.e. very early in the morning or late at night, with concrete being the ‘coolest’ possible, aggregates stored in shadow etc.
Concrete curing in frost:
Normally concrete must not be casted in extremely low temperatures, however when this is un- avoidable e.g. sudden drop of the temperature below zero, its free surface must be covered with concrete curing blankets. These are made out of thermo insulating materials like rolls or plates of rockwool, glasswool with aluminum covering, polystyrene boards later used in insulations. In that way, we can make use of the concrete’s own heat. The blankets must be secured from wind up-turnings with e.g. rafters and balks. If the temperature drops too low, heaters like the ones used in out-door coffee shops may be used with their reflectors in an inverted position. In the past, barrels with fire were usually placed underneath the formwork; they contained sand wet with oil.
In areas exposed to extremely low temperatures, the use of air–entraining admixtures or addi- tives is mandatory in order to protect the concrete from the catastrophic results of frost.
Removing the formwork
The following table presents the minimum time requirements before removing the formwork. It regards typical constructions for usual temperatures:
Constructional elements |
Cement strength |
|
32.5 |
42.5 |
|
Lateral sides of beams’, slabs’, columns’, shear walls’ formworks |
3 days |
2 days |
Slabs’ formworks and beam span formworks when the span is lesser than 5 m |
8 days |
5 days |
Slabs’ formworks and beam span formworks when span is greater than 5 m |
16 days |
10 days |
Safety columns of frame beams and slabs with a span greater than 5 m |
28 days |
28 days |
Nowadays, cement with 32.5 strength comes only in sacks. On the contrary, the cement used by most concrete production industries usually has strength equal to 42.5.
When removing the formwork of slab or a beam 5 days after concreting and intending to cast the next floor-which means doubling the loads applied to the floor without formwork – supporting scaffolds (falsework) must be placed beneath the formwork-free floor. This problem is much more critical in cantilever slabs.
General note:
It must be mentioned that there are a lot of exceptions to the above summarized rules where the suggested limits of most issues may be exceeded. However, in every case the supervisor engineer is responsible for satisfying the general or special specifications of the work.
Self-compacting (self consolidating) concrete
The science dealing with construction materials has created a new type of concrete, the self- compacting or self-consolidating concrete which is ideal for earthquake resistant structures that have narrow spaced reinforcement. It is a kind of ‘gravel-concrete’ (with aggregates ranging from 12 to 14mm). It contains 4th generation plasticizers and has a strength equal or greater than C25/30. Its slump height is far greater than the S5 class (therefore its workability is deter- mined by the spread test). It literally flows inside the formwork and it does not need vibration!