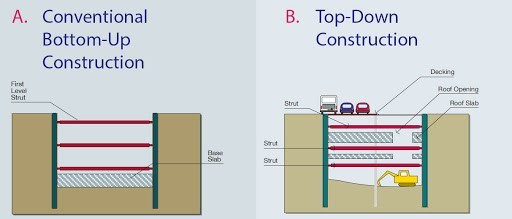
TOP Down & Bottom Up Construction Methods
When it comes to excavations for major projects, particularly in densely developed urban areas, there are more options than just the conventional bottom-up building approach
While just about every major construction project involves digging large holes in the ground, the methods of excavation can have a significant impact on timeframes and costs. The majority of large-scale projects have opted for a conventional ‘bottom-up’ approach, but there are very powerful arguments for considering other options by using the ‘top-down’ method, or a hybrid which combines ‘bottom up’ and ‘top down’. This combined method is gaining more traction because it can be highly competitive in cost and time.
Approaches for deep excavation explained
Bottom up – this conventional method involves first sinking temporary diaphragm walls to the required depth below ground, digging and removing soil, installing temporary steel strutting and then creating the complete hole with a concrete slab base and open to the sky. As the name suggests, the building work then rises from the concrete slab base. Necessarily, there is a lengthy period of time during the excavation in which construction cannot take place.
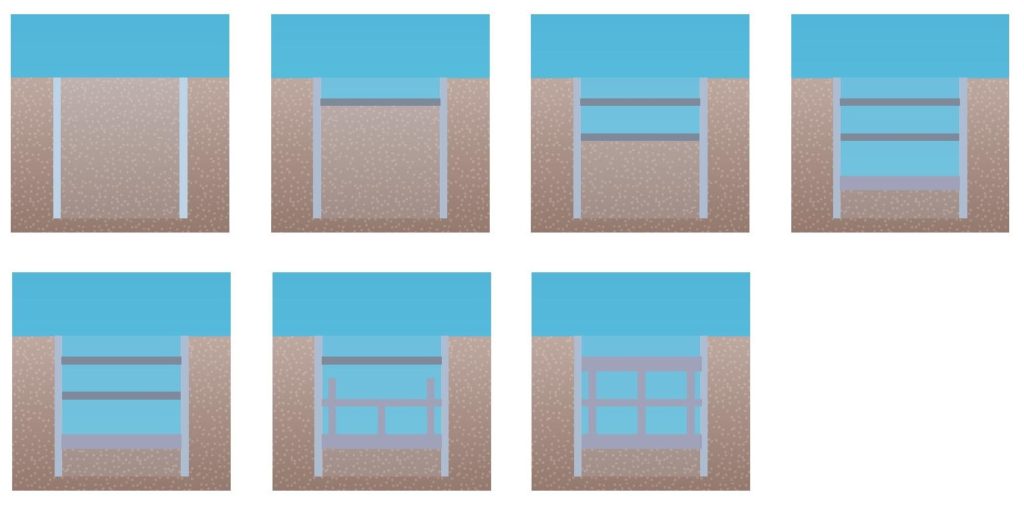
Top down – once again the project begins by sinking the diaphragm walls, plus central supporting ‘plunge’ columns (can be temporary or permanent), and then excavating enough of the earth to complete a ground-level slab. This slab is substantial enough to carry the weight of construction equipment including cranes, and incorporates openings though which soil can be lifted up and removed. The excavation then takes place under the ground slab, and permanent floors are cast on the way down to the desired depth. It also means that simultaneously construction above ground can start. This is ideal for high-rise structures in constrained sites and can result in time savings that can amount to several months. Cost savings are available too because generally no steel strutting is required for wall support. Top-down construction uses the permanent structure floors to strut as the excavation is taken down in stages, floor by floor. Another use of the top-down approach is when creating new metro lines under roads. In these cases it’s possible to use the top slab to safely carry all utilities and some of the road can be reinstated until the works underneath have been completed.
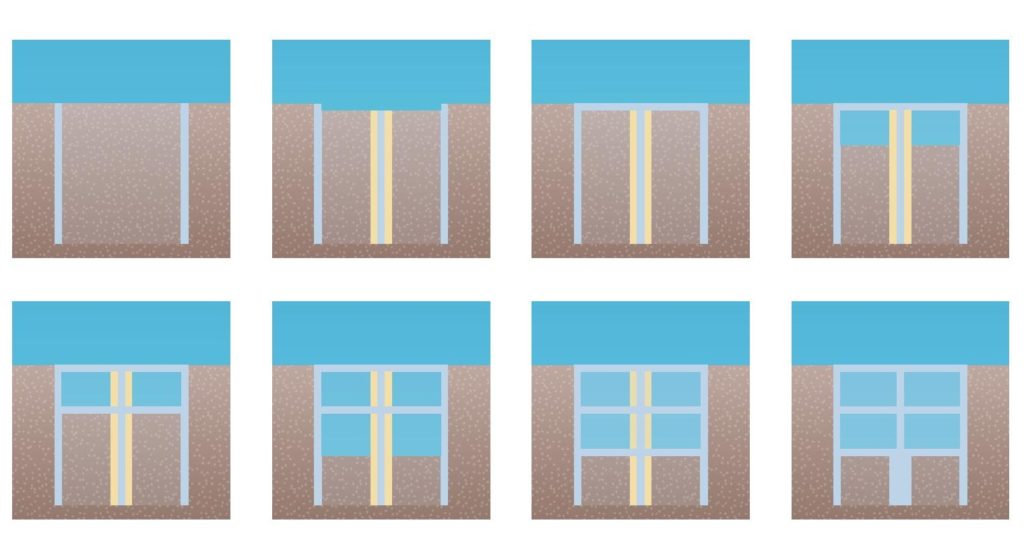
Hybrid method – this is when it is appropriate and the site is large enough to incorporate both methods. The concept is that part of the site is dedicated to a top-down approach while the rest is built from the bottom upwards.
Compare and contrast
Top-down approach
Advantages | Disadvantages |
· This offers very quick site coverage which includes a robust working platform.· For large sites, openings can be provided in the floors at many locations within the site and not just around the perimeter.· For smaller sites, the ground floor structure provides a site working area and a temporary steel decking is not required.· Requires little or no temporary steel shoring – producing good cost savings.· Requires no formwork for floors or roof with significant savings in cost and time· Cheaper to construct.· Multiple accesses made possible through the voids in the slab and not limited to around the perimeter.· For combined development that includes a substantial structure above ground, the top-down approach makes it possible to get an early start on construction.· For sites of irregular shape, floor slabs are more versatile and therefore are more efficient than using steel strutting | · Because work needs to be carried out through openings in the slab, access is only via the openings below the slabs during excavation.· When building multiple stories above ground, this approach requires the construction of strong foundations and plunge piles· In the case of very tall buildings, this approach requires complex design work – for example it may require plunge piles sufficient to support the first 10 floors above ground, but then more work will be required to create more substantial foundations for floors above the first 10.· Waterproofing cannot be installed outside the diaphragm walls. |
Bottom-up approach
Advantages | Disadvantages |
· Design is easier and therefore design costs are lower than for the top-down approach, and a bottom-up approach is quicker to design.· Heavy foundations, such as large piled foundations for the high rise are required and are generally installed from the ground surface before excavation for top down and for bottom up.· Waterproofing can be installed around the whole outside, including the outside the permanent walls.· Access for cranes is not restricted up and down the sides of the excavation. For sites large enough to have a perimeter area to accommodate construction equipment, and when the excavation is not wide then this method is quicker than the top-down approach. An example here is that some metro stations have a large site area outside that is handed back for other uses. | · Construction is usually slower and more expensive than the top-down approach.· It is not possible to carry out simultaneous upwards and downwards construction until the bottom of the basement is concreted.· Cranes can be located only on firm ground outside the excavation or on heavy-capacity temporary decks within the excavated area. For wide sites cranes may not be able to reach the middle of the excavation, whereas the top-down method can provide openings at many locations across the site area.· For very deep projects, the thickness of the temporary walls plus the permanent walls is greater than for the top-down method using diaphragm walls plus skin wall. Therefore, bottom-up working needs more space for the combined walls or the finished floor area is smaller.· The temporary walls serve little or no purpose after completion and, therefore, are wasted.· If the scheme design is for bottom-up construction, the time for tendering might be longer since contractors need to prepare a tender design. |
Current above and below grade construction
Conventionally, buildings with underground basements are built by bottom-up method where sub-structure and super-structure floors are constructed sequentially from the bottom of the sub-structure or lowest level of basement to the top of the super-structure. Though this conventional method, also called as bottom-up method, is simple in both design and construction, it is not feasible for the gigantic projects with limited construction time and/or with site constraints. Top-down construction method as the name implies, is a construction method, which builds the permanent structure members of the basement along with the excavation from the top to the bottom. Top-down method is mainly used for two types of urban structures, tall buildings with deep basements and underground structures such as car parks, underpasses and subway stations. In this case the basement floors are constructed as the excavation progresses. The top/down method has been used for deep excavation projects where tieback installation was not feasible and soil movements had to be minimized. Top-down construction method which provides the significant saving of the overall construction time has been adopted for some major projects where time factor is of primary importance. The sequence construction begins with retaining wall installation and then load-bearing elements that will carry the future super-structure. The basement columns (typically steel beams) are constructed before any excavation takes place and rest on the load bearing elements. These load bearing elements are typically concrete barrettes constructed under slurry (or caissons).
PROCEDURE
The typical construction procedure of top down construction is as follows·
- Construct the retaining wall.·
- Construct piles. Place the steel columns or stanchions where the piles are constructed.·
- Proceed to the first stage of excavation.
- Cast the floor slab of first basement level·
- Begin to construct the superstructure·
- Proceed to the second stage of excavation; cast the floor slab of the second basement level.·
- Repeat the same procedure till the desired depth is reached·
- Construct the foundation slab and ground beams, etc. Complete the basement·
- Keep constructing the superstructure till it gets finished.
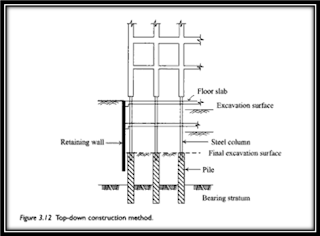
INSTALLATION OF RETAINING WALL
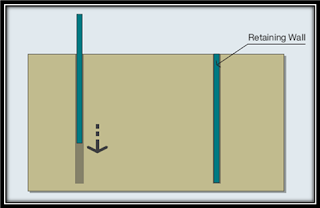
The underground retaining wall which is usually a diaphragm wall, is installed before excavation commences.Excavation and installation of steel strut
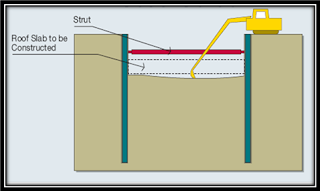
The soil is excavated just below roof slab level of the underground structure. Struts are installed to support the retaining walls, which in turn support the soil at the sides
Construction of underground structure
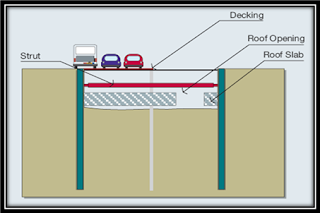
The roof slab is constructed, with access openings provided on the slab for works to proceed downwards. The roof slabs not only provides a massive support across the .
Construction of underground structure
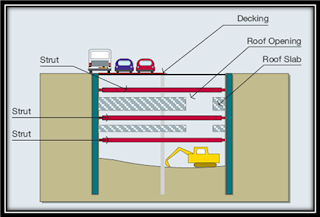
The next level of slab is constructed, and this process progresses downwards till the base slab is completedConstruction of underground structure
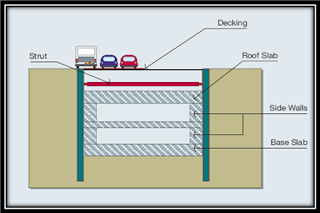
The side walls are constructed upwards, followed by removal of the intermediate struts. The access openings on the roof slab are then sealed.
Backfilling and reinstatement
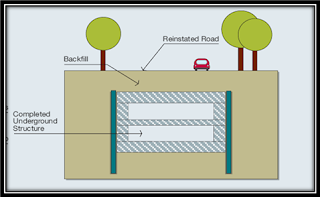
After the underground structure is completed, the soil is backfilled to the top strut level before the strut is removed. This is followed by completely backfilling the top of the underground structure and finally reinstating the surface areas.
Tip: