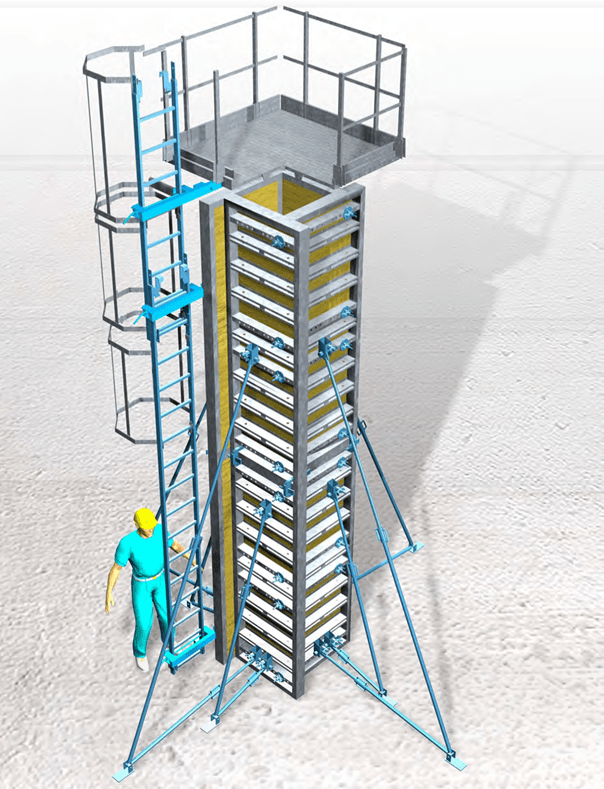
The moulds
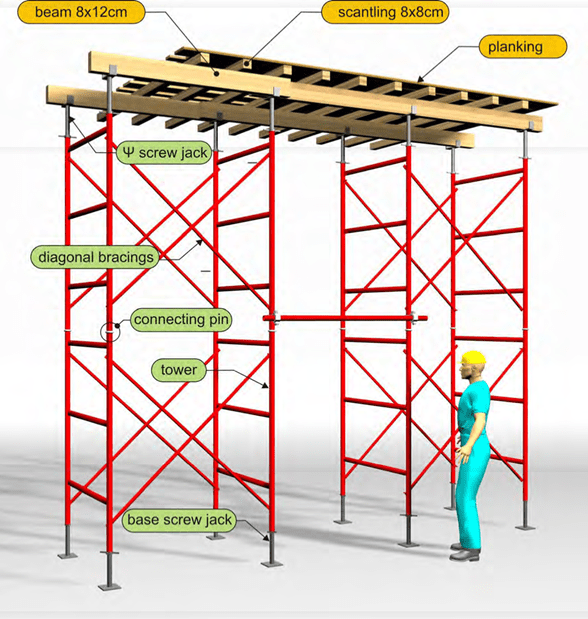
The elements of the moulds used for the formation of structural reinforced concrete members are separated in four categories:
- Surface elements or planking
- Horizontal bearing elements or beams
- Scaffolds or staging
- Accessories like connectors
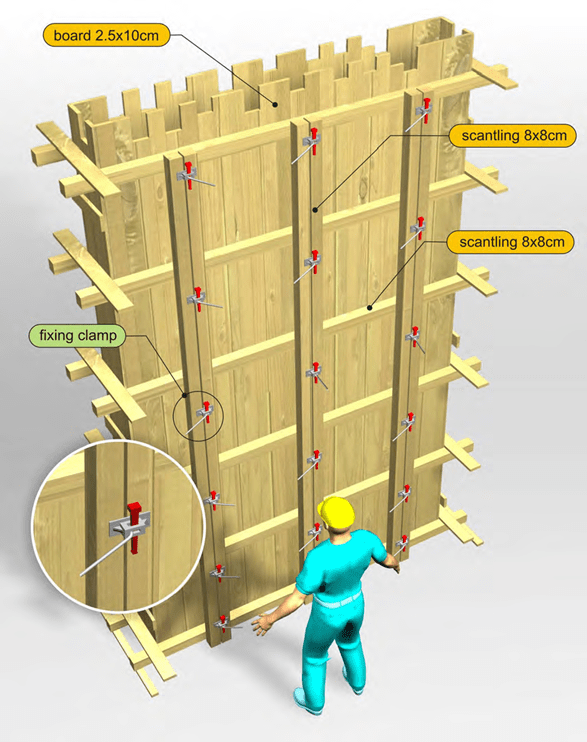
The mould elements might be conventional or industrialized. The former are mainly made out of natural timber and based on their section dimensions they are called:
- boards with a usual thickness of 22mm, width ranging from 8 to 15cm, and length vary- ing between 2.30 and 4.50m
-
scantling (wooden joist) with a typical cross-section 8x8cm and lengths ranging from
2.40 up to 4.50m
-
beam with a usual cross-section from 8 to 12cm x 12 to 20cm in different lengths from
2.50 up to 5.00m
- shuttering plywood with thickness ranging from 18 to 25mm, width 1.25m and length 2.50m
- plank or balk with 5.0 cm thickness, width varying from 20 to 30 cm and length 4.0m.
The elements of a conventional scaffold are made out of hollow steel sections with a usual di- ameter around Φ50. These sections are used for the formation of the standards and the frames.
Frames usually have a height ranging between 1.20 and 2.50m but when combined with the base screw jack and the upper “Ψ-shaped” screw jack, they may reach almost any height. Generally frames are vertically tied together with the use of diagonal bracings made out of hol- low steel sections varying between Φ25 and Φ30 thus forming the towers.
The accessories of column moulds secure the position of the lateral elements against the “hy- drostatic” pressures applied during casting. The most intense problem appears in columns and shear walls because of their large height and consequently because of the high lateral pres- sures that appear. The connectors are usually made out of steel, they have an adjustable length and they are placed every 20 to 50cm.
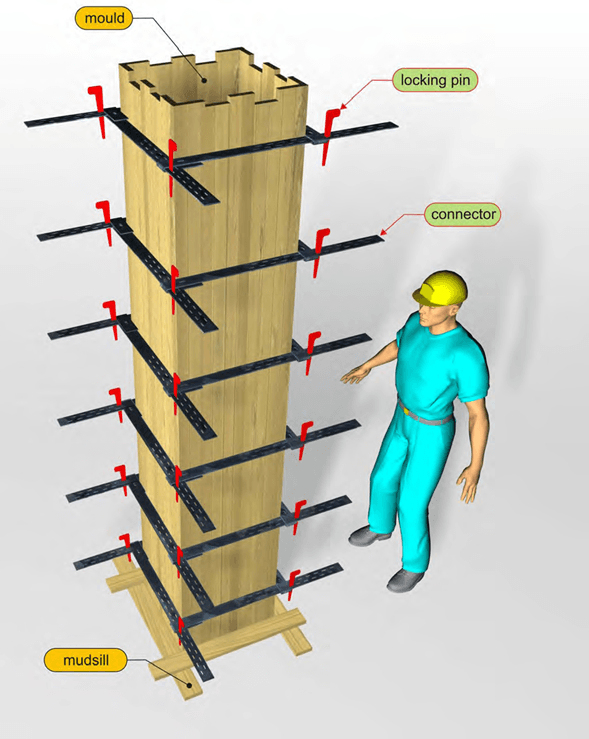
Industrial formworks are a combination of timber, steel, aluminum and plastic and their names vary according to their production industry.
The advantages of industrial formworks:
- high construction quality
- small amount of required personnel
- fast implementation
- civilized working conditions
- personnel security
- achievement of smooth surfaces that do not require finishing
The disadvantages of industrial formworks:
- high initial investment cost
- the need to have a detailed and accurate implementation design in every work
- the need for crane usage
- the created smooth surfaces lower the adhesion between the concrete substrate and the finishing
- low flexibility in small and complex constructions
By comparing the advantages and disadvantages and their corresponding importance, we fi- nally conclude in the indisputable superiority of the industrial formworks against the conven- tional formworks. Taking into consideration that the use of self-compacting concrete (see § 2.4.9) will probably predominate in the construction of earthquake resistant structures, the in- dustrial formworks are the ideal solution since it can adequately bear the large pressures ap- plied to the inside of the mould.
The following figures show three cases where industrial formworks are being used. In all three cases the common characteristic is the large height of the structural element.
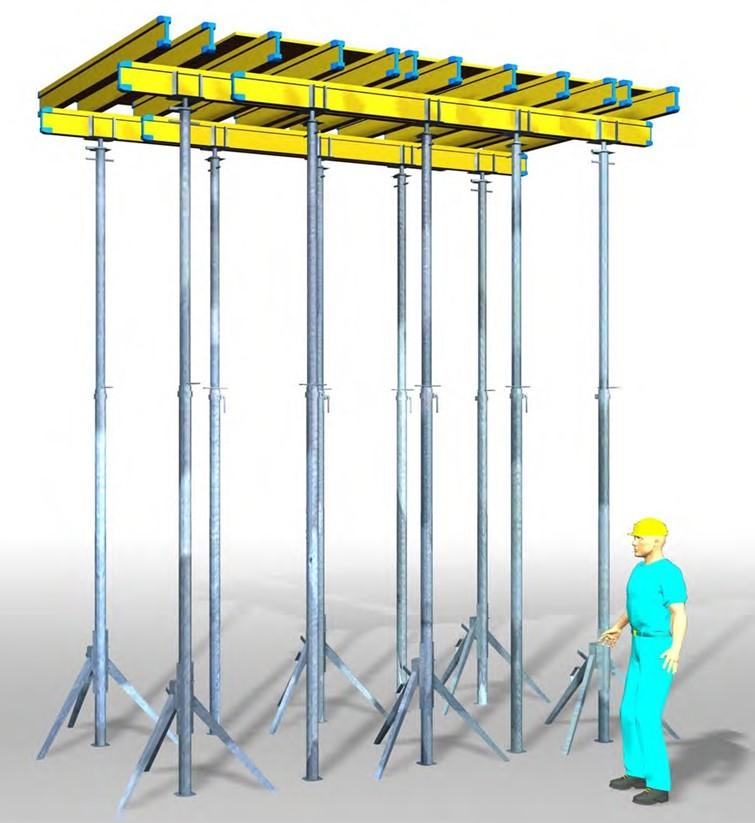
Industrial scaffold for the formation of slab’s formwork 1
The construction of the beams’ and slabs’ formwork is performed with the use of composite, tim- ber T-section beams and shuttering plywood without nailing. Scaffolds are made out of alumi- num. Formwork dismantling is performed by releasing the special pins at the top of the scaffold, that way it controllably recedes around 5cm without damages and without danger of accident.
1 In areas with low seismic activity the industrial formworks, based on their specifications, may reach up to 5.50m high without needing diagonal bracings. In earthquake prone regions, in order to face a possible seismic event either during the casting or during the curing process, it is suggested to use the same scaffolds according to their specifications, providing that all columns are constructed in order for the scaffolds to be tied upon them (see and § 2.4.5).
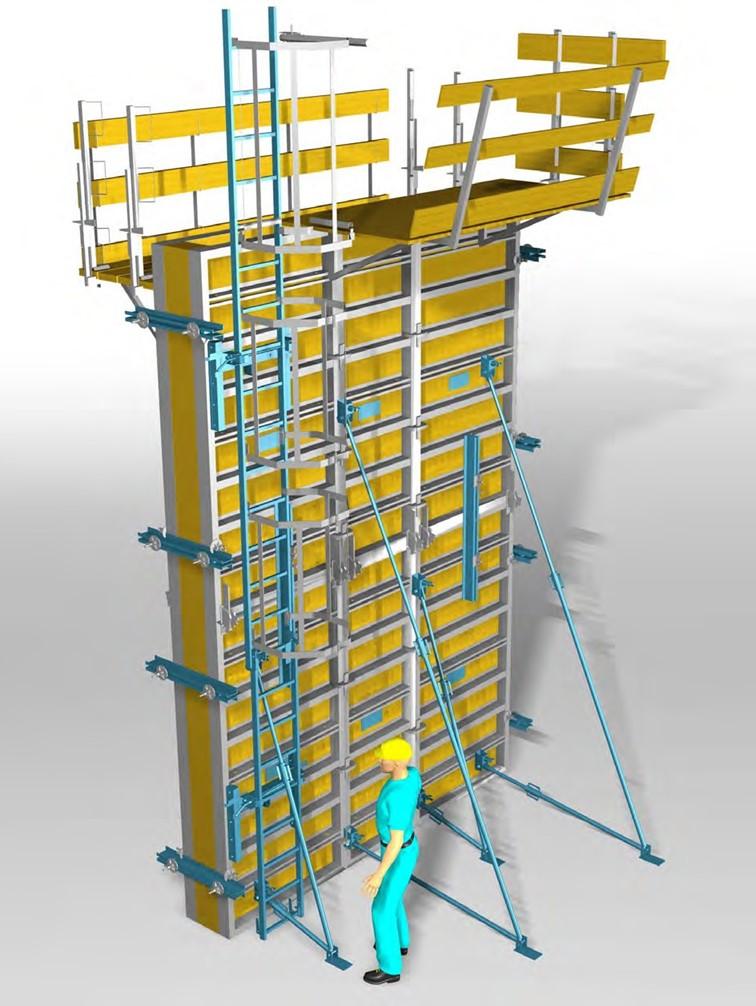
Shear wall moulding with the use of industrial metalwork
Assembling the formwork of a 5.50m high shear wall and positioning the working platform re- quires only a few minutes. Removing that formwork requires even less time and it is a fast and safe procedure.
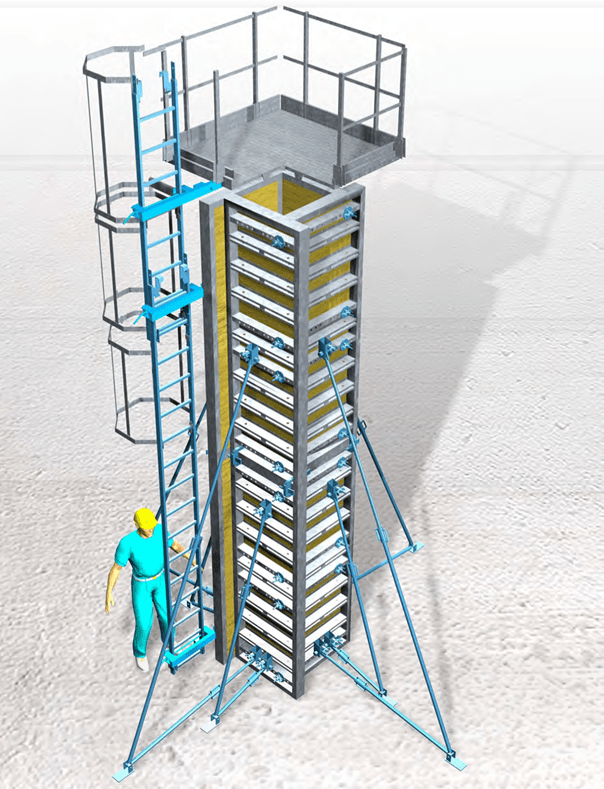
Column moulding with the use of industrial metalwork
This column is 5.50 m high and its formwork is quickly created by assembling formwork pieces with dimensions divided by 5cm. These pieces are tied together with butterfly valves, placed in predefined positions. The formwork is temporarily supported by light-weight diagonal struts. The working platform at the top as well as the ladder are being placed and removed within a few mi- nutes.
If the surfaces of the shear walls, beams and slabs are going to be plastered it is mandatory to wash them well by means of pressure pumps in the order of 100 atmospheres followed by all the necessary practices in order to increase the adhesion between the substrate and the plas- ter.
In cases of particularly careful industrial formwork implementations, it is remarkable how the fi- nal plastering might be avoided due to the excellent and ready for coloration surface.
Note:
The use of moulds made out of water-resistant cupboard, metal sheet or plastic leads to the fineness and more economical construction of circular columns.