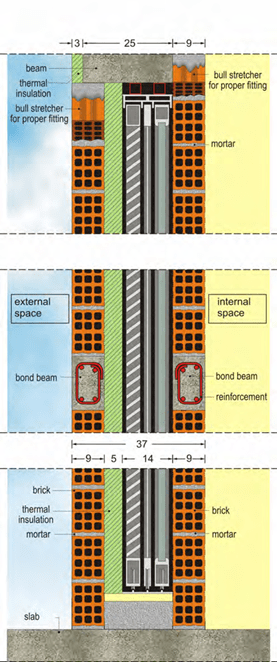
Thermal insulation of structural elements
When the thermal insulation is embedded inside the exterior or the interior shell of the building and it is independent of the structural frame’s construction, the solution is clear and most of all effective. However, when the thermal insulation is placed upon the exterior or the interior sur- face of the structural frame as part of the total thermal insulation e.g. in buildings with masonry walls, various issues arise. These include thermal bridges and constructional matters regard- ing antiseismic behavior.
This paragraph deals with the cases where the concrete elements’ thermal insulation is embed- ded in the structural frame. In masonry infills thermal insulation is usually placed inside the ma- sonry walls.
Generally, the structural elements of the frame are thermally insulated by the use of extruded polystyrene boards2 with thickness ranging from 3 to 5 cm. These boards have ribbed surfaces for better adhesion both with the concrete substrate as well as with the plaster that will cover the final surface.
If the energy/bioclimatic design of the building requires the contribution of the structural frame’s heat capacity (this is the common case in residential buildings) then the thermal insulation is placed upon the external surfaces of the structural elements.
In shear walls, columns and beams the thermal insulating boards are placed upon the element’s surface that is on the outer face of the structure. On the other hand, in slabs, most of the times, it is preferable to place them on the bottom side. This is the best solution both from a practical and an energy point of view. However, it may not be ideal for the upper floor slabs.
If the thermal insulating boards are placed on the lower side of the slab and the surface is going to be plastered, it is recommended to place, prior to plastering, a light-weight flexible composite mesh e.g. glass mesh to prevent plaster cracking especially in the joint areas of the boards and the concrete or the walls.
2 The minimum required thickness of the extruded polystyrene is based upon the coefficient of thermal conductivity λ and generally upon the thermal insulation design. When using environmental friendly materials, the minimum thickness of the thermal insulating board is around 4cm.
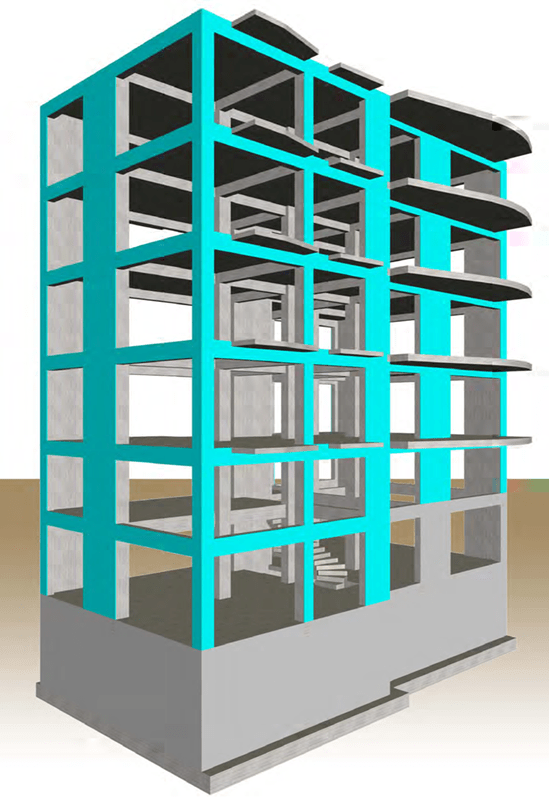
Representation of the thermal insulated frame of a building
<project: bkΙnsulationGR 3>
3 The project<bkInsulationGR>, is an altered version of the project <bkGR>, due to its size, it runs only in the professional software.
Placing the thermal insulating boards to the exterior surface of the concrete elements creates one problem; it sets limitations to the proper fitting of bricks in the external masonry walls.
Some of the practices followed when building masonry infills are shown below.
The choice of the most suitable solution depends upon the importance of factors such as: the brick fitting near columns and beams, the formation or not of an edge between the beam and the wall, the weight of the wall, the space they take, the cost.
Typical solutions in exterior masonry walls
(by using 9x12x19 bricks)
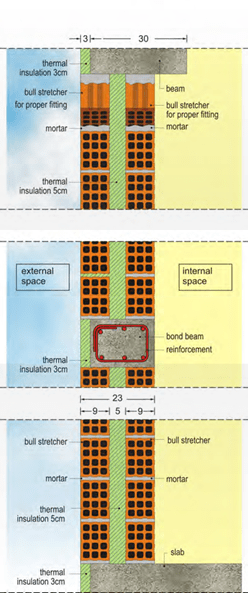
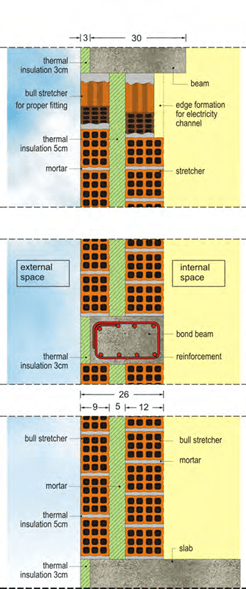
External blind wall with 2 bull stretchers
External blind wall with 1 bull stretcher and 1 stretcher
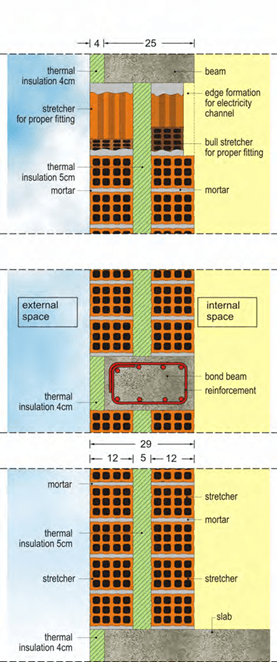
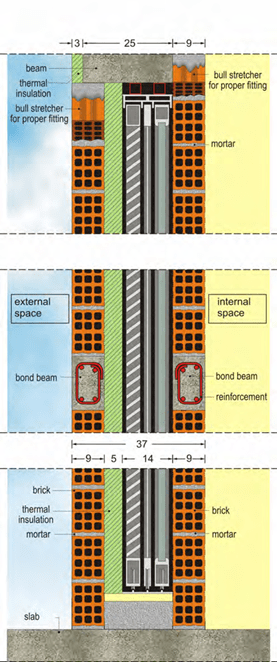
Eternal blind wall with 2 stretchers External wall with sliding frame
Notes:
-
In areas where the used bricks have different dimensions from the ones mentioned above, corresponding practices and rules apply.
-
The 12cm thick wall when compared to the one with a thickness equal to 9cm, has disad- vantages like a higher cost, a larger weight and a 12-9=3cm limitation of the interior space. On the other hand, it has advantages like the better brick fitting, the higher heat capacity (of the layer towards the inner face) and the possibility to embed electrical piping.
-
When it is important for the beam and the masonry to have exactly the same width (no edge formation), apart from the other solutions, a free space may be left between the thermal in- sulation board and the wall.
-
When an edge is formed between the beam and the wall, it is preferred to have a large width rather than a small one.
-
Based on the type of the electrical installation, we must allow space for the cable piping that will pass through the structural frame or/and the wall.
-
A simple way to create channels in the support faces of beams and columns is the use of a board or an extruded polystyrene strip 2cm thick and 10 cm long.
-
Frequently the real brick dimensions differ from those of standardization. For instance, nine times out of ten, the bricks with nominal dimensions 9x12x19 have real dimensions equal to 8.5×11.5×18.5.On the other hand, the beam’s dimensions are usually correct.
-
A typical bond beam reinforcement is: stirrups Φ5/10 or Φ6/15 and upper, lower longitudinal reinforcement 2 to 4 Φ10 rebars (depended upon the bond beam’s width). The steel class may be B500A.
-
Bond beams’ rebars might end before meeting the columns or they may get anchored inside
them.
-
The most practical way to anchor the bond beams’ rebars inside the columns is by creating holes to the column sides and implanting starter bars by means of resin adhesives.
Rules for choosing the correct thermal insulation thickness for the structural frame
As far as the thermal insulation efficiency is concerned, the necessary thickness is defined by the corresponding design, however constructional difficulties must be always taken into ac- count.
As far as the proper masonry fitting is concerned, a good solution is to use thermal insulation 3 cm thick in both columns and beams.
As far as the reinforcement imple-
mentation is concerned, it is sug- gested to use thicker thermal insula- tion in columns than in beams. As a result, the corner bars of the beams will be anchored, unobstructed, in- side the column’s mass, as shown in the vertical beam of the figure, in contrast to the horizontal beam of the same figure, where the edge rebars of the beam have to be bent.
As far as the standardization of the
columns’ and beams’ width is con-
cerned, the use of 5cm thick thermal insulating boards helps both in the
increase of the thermal insulation efficiency and in the standardization of the structural ele- ments’ dimensions in integer multiples of 5cm. However, this creates difficulties in the proper fitting of bricks in external walls. Usage of 9cm bricks instead of 12cm eliminates this problem.
Based upon all the above, an optimal technical solution is to use 3cm thick thermal insulating boards in the columns and 5cm thick boards in the beams. Moreover, the masonry should be built externally with thickness equal to 12cm.

Constructional problems
When a floor does not require thermal insulation e.g. pilotis or basement, extra attention must be paid to the vertical centering of columns so as to avoid having the columns of one floor placed outside the perimeter of the columns that belong to another floor. The next fig- ure shows two columns that have a total cross-section 40/40, however, in the upper floor, the column has a 37/37 cross-section and a thermal insulation board with 3cm thickness.
These cases are usually met around the perimeter of
the building, in pilotis, in basements or in semi-open floors, when the thermal insulation is placed to the outer face of the structures (as it should in most cases). The created problem may be solved with various ways:
1st Solution: Construct a column greater in size and with larger stirrups.
Drawbacks: The drawback in following this solution is the ec- centricity of the column’s rebars and the need for bending them up at a large angle, something that entails a high degree of constructional difficulty.
Application: This solution applies to all cases.


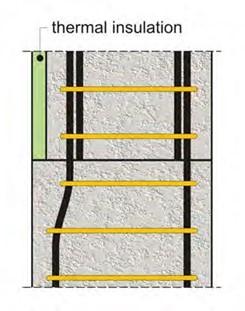
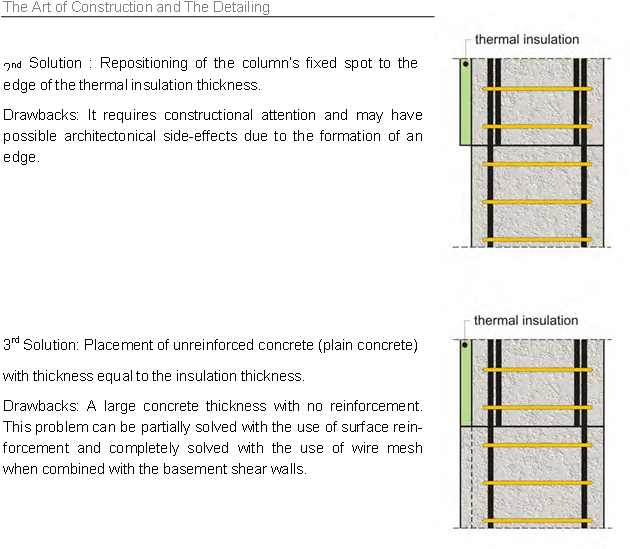
Note:
An economical and constructional simple way to efficiently insulate a building and face fewer local problems in the structural frame, is to place the entire insulation at the external face of the building after the completion of the load bearing frame and the masonry walls. That way, a thermal insulating shell, e.g. 5cm thick is formed circumferentially in all exterior surfaces (con- crete and masonry). The placement of this ‘blanket’ is being done after the construction of the structural frame and the masonry walls without thermal insulation. This specific solution, due to the formation of fewer thermal bridges, has the maximum energy efficiency and the advantage of that it can be replaced at any time. Like every other technological solution, the above men- tioned method is contrary to traditional practices that regarded peripheral walls as monolithic elements, with plaster covering that determined the architectural character of the building. Of course times change and little by little energy changes become dominant, moreover the material science provides new ways of architectural expression that can be adapted to the local condi- tions of each region.